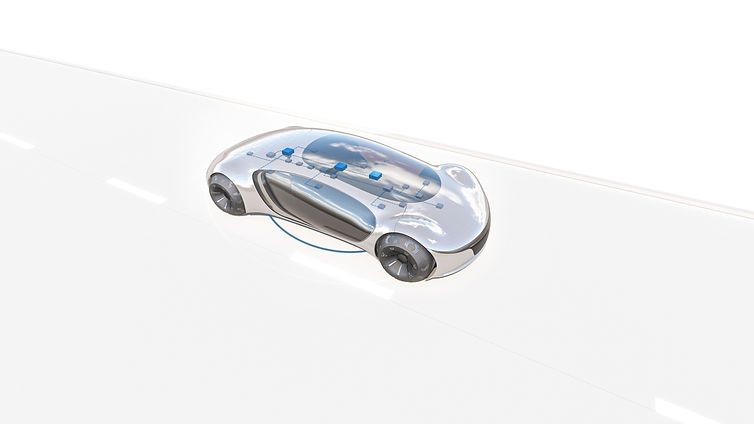
Hardware
Design
State-of-the-art multicore technology and housings
We offer professional and customized analog and digital hardware design services for complex embedded electronics projects in the electric vehicle industry. Our expertise allows us to design custom PCBAs, integrate off-the-shelf solutions, and deliver innovative and cost-effective solutions. We prioritize flexibility and tailored approaches to meet the unique requirements of each client, ensuring optimal performance, efficiency, and quick turnaround times.
-
Printed Circuit Board (PCB) Design
-
High and Low Voltage Design
-
Circuit Design at both Micro and Power Levels
-
Component Development
-
Design and Product Validation
-
Design Failure Mode and Effects Analysis (FMEA)
-
Electromagnetic Compatibility (EMC) Test
With a strong commitment to quality and a deep understanding of the evolving electric mobility landscape, MEAtec is dedicated to empowering our partners to excel and thrive in this exciting industry.
PBC Trends in the Automotive Industry
The PCB industry has evolved in parallel with the development of electronic components and demand for increased functionality and improved performance. They have made significant progress in material selection, design and manufacturing techniques and tools such as microvia technology, autorouter, and autoplacer, which allows to control the component placement process to achieve miniaturization for higher functionality in less space.
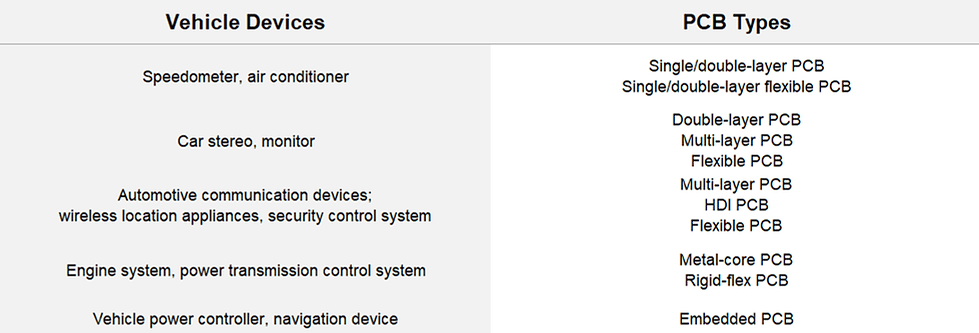
This resulted in the development of specialized PCBs with various features such as flexible, rigid-flex, high-density interconnect (HDI), and high-speed, among others. Especially high-speed PCBs are one of the fastest growing subgroups in industry due to their ability to carry signals at high frequencies with minimal distortion and loss. They require special design considerations such as signal integrity, controlled impedance, ground planes, and materials, and are critical components in applications such as battery management systems, motor control units, and communication systems in electric vehicles.
In order to meet the stringent requirements of space, weight and cost, MEAtec supports its partners with PCB designs with state-of-the-art components and suitable materials.
Future Technology: Super Computers for Vehicles
In today’s vehicle systems are often managed by decentralized control units, which make the vehicle E/E architecture complicated. High-performance computing (HPC) involves consolidating vehicle intelligence into a few high-performance central computers within the vehicle, rather than distributing it among numerous microcontroller. This centralized approach allows for more efficient management of vehicle systems, lowering energy usage, minimizing the need for multiple control units and associated cables, and providing design flexibility, make maintenance easier.
HPC is a vital component in developing and implementing advanced vehicle systems that ensure safe, reliable, and efficient performance. This centralized technology enables vehicles to quickly and accurately respond to changes in their environment by processing large amounts of data in real-time, a critical requirement for ADAS and autonomous driving. Moreover, parallel processing enables systems to perform multiple calculations simultaneously, improving performance and data processing speed. This capability is especially important for V2V communication, where vehicles need to exchange large amounts of data quickly and efficiently. In addition, this technology enables vehicles to stay up to date even years after their purchase, as software updates can be easily implemented on the central computer rather than having to update multiple ECUs.


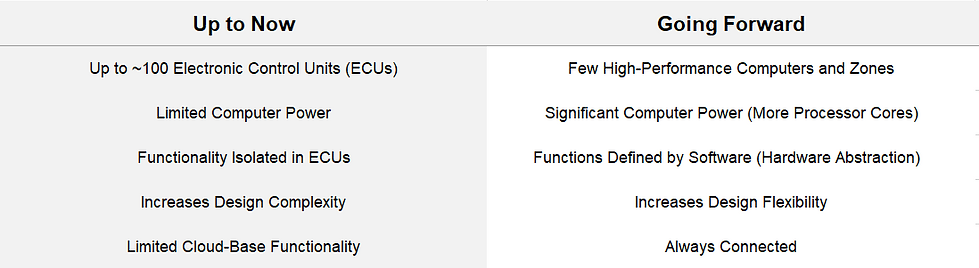
Testing for Electromagnetic Compatibility
Emissions from digital circuits are one of the biggest electromagnetic interference (EMI) problems facing today’s designer of vehicular electronics. The automotive industry and individual automakers must comply with various requirements to ensure the safe and reliable operation of electronic systems. These requirements include limiting excessive EMI or noise emission from electronic systems and ensuring immunity to noise emitted by other systems.

Automotive emission requirements are aimed at protecting onboard receivers (CISPR 25) and immunity requirements are very stringent to protect the safety-critical onboard devices. When designing an electronic circuit, it is necessary to take several precautions to ensure that its EMC performance requirements can be achieved. To avoid issues in vehicles, several techniques and procedures are used like keeping loops small, good impedance matching, shielding, short ground connections, using bypass capacitors, supply line inductors and spread-spectrum clocking.

With the support of our expert engineer team, we can design robust systems that ensure EMC-compliant operation of automotive systems.
Design Failure Mode and Effects Analysis (DFMEA)
Systematic step-by-step failure analysis technique used through the design and production process to identify where failures can occur, how frequently they could happen and whether or not we can detect them. It evaluates processes for possible failure and to prevent them by correcting the process rather than reacting to effects after failure has occurred. MEAtec provides its partners with design failure mode and effect analysis support, which allows failures to be detected as early as possible and thus corrected without significant cost and time loss.

Design Failure Mode and Effects Analysis (DFMEA) is first done by identifying all the components of vehicle. This is followed by identifying failure modes for each component, its causes and its effects on the individual component and the vehicle as a whole. After that, severity of the failure, likelihood of occurrence of failure and likelihood of detection the failure is determined for each failure mode and rating from 1 to 10. The ratings are multiplied to calculate an index called Risk Priority Number (RPN). After the RPN is calculated the failure modes of components are prioritized according to the obtained RPN and identify actions to improvement.